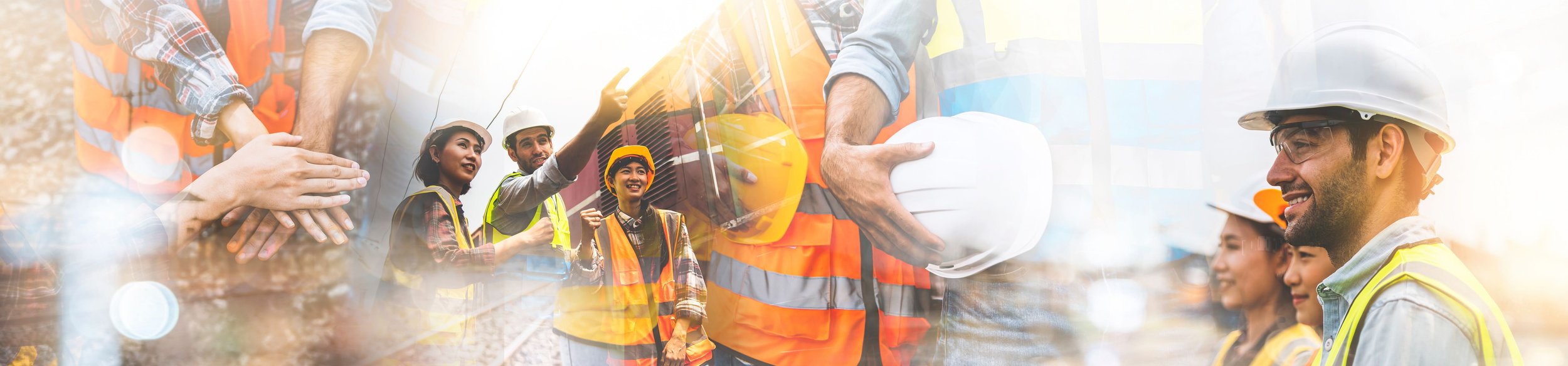
Own Every Moment, Crush Every Risk
Incident Management
Picture this clearly
Production stops: When your line halts, you’re burning between $10K to $100K every hour. A spill isn’t just a spill—it’s cash bleeding from your bottom line.
Worker safety. In the last decade, OSHA recorded 2,607 fatalities in manufacturing settings. A delayed response isn’t paperwork—it’s people’s lives, morale, and trust at stake.
Legal nightmares: OSHA fines aren’t small inconveniences—they range up to $145,000 per violation. Mismanaged incidents quickly escalate from fines into lawsuits or forced shutdowns.
Reputation implosion. A single incident shouts “negligence” and key clients, such as major automotive OEMs, quickly pivot to safer partners. Once lost, that trust rarely returns.
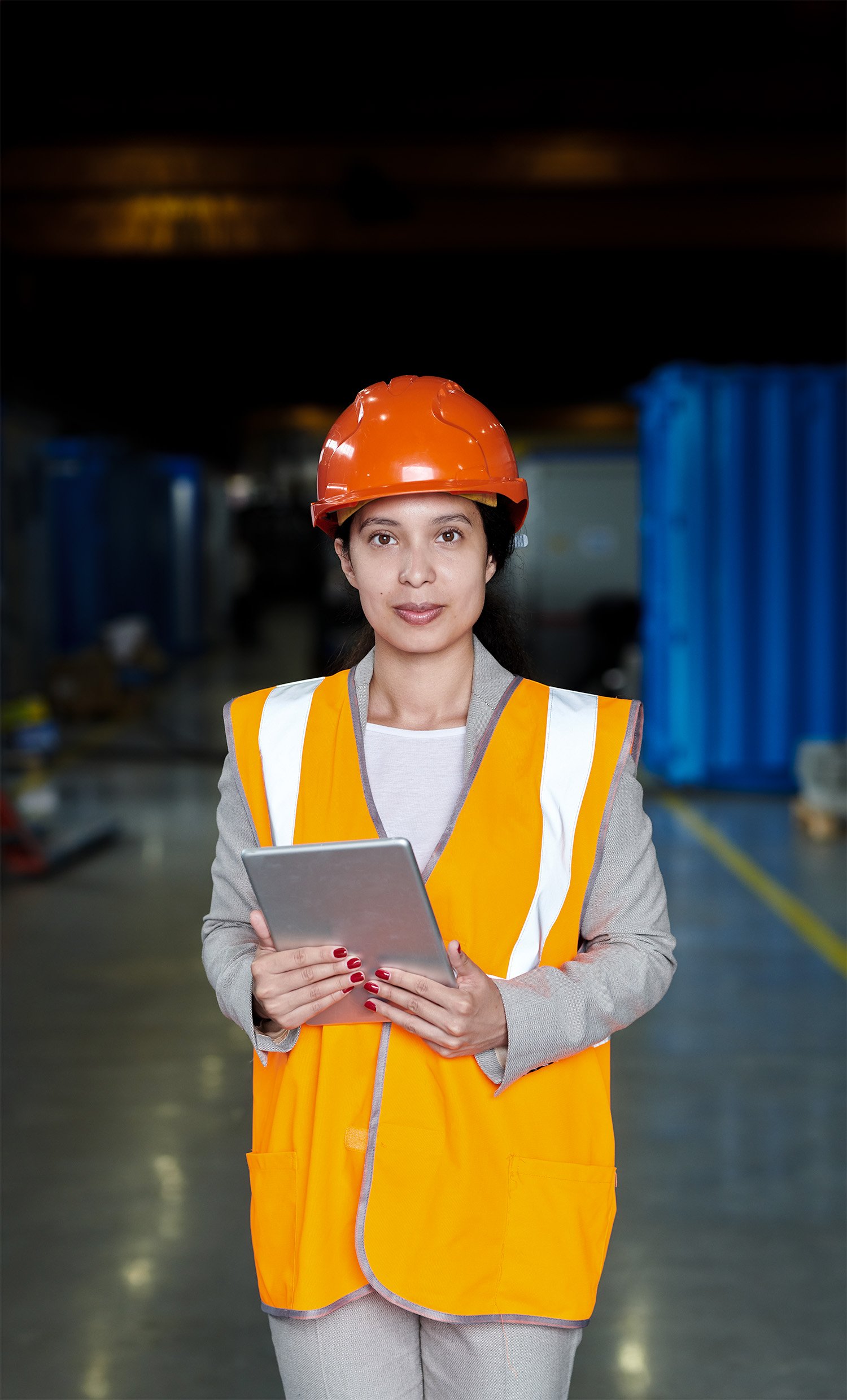
Less than 2 hours
At Timpl, incident management isn’t a passive log entry—it’s a rapid, coordinated strike. We don’t just “manage” incidents; we own them, immediately and thoroughly.
From the moment an incident happens, we commit to investigating, documenting, reporting, and implementing corrective actions within two hours or less—achieving this 95% of the time. That speed is no accident; it’s embedded in our systems, training, and mindset.
Crystal-clear communication. Transparent documentation shows exactly how incidents are handled, reinforcing trust with OSHA inspectors and clients.
Real-time, floor-level response. Our trained supervisors react the instant an issue arises: isolating hazards, securing danger zones, containing the problem before it spreads, and restoring safety fast. Every second we save protects your people, your production, and your reputation.
Proactive prevention. We don’t just respond; we anticipate. Our 4M approach (Man, Machine, Material, Method) identifies hazards before they occur, dramatically reducing future incidents.
We Don’t Just React. We Fix the Core.
People First, Always
Unsafe behaviors aren’t ignored. If an incident traces back to repeated risky actions, we coach immediately. If that fails, we recommend swift replacement. Safety isn’t about second chances when lives and production are at stake—it’s about setting and enforcing standards, every shift.
Hazardous Material Response on Command
Chemical spill? Combustible dust hazard? Our teams act immediately—isolating, neutralizing, and reporting hazardous material incidents before they spiral. We treat every material-related event like a ticking clock, moving faster than the risk can escalate.
Methodical, Relentless Incident Response.
Every incident triggers a strict escalation process: we isolate and contain the hazard immediately, investigate on the floor with real-time interviews and photographic documentation, perform a full root cause analysis, and apply corrective actions—all within two hours. No shortcuts. No delays. Every step is disciplined, recorded, and resolved fast becaus hesitation costs more than time; it costs trust, money, and lives.
Machines Don’t Wait, and Neither Do We
We catch trouble before it shuts you down. Our routine machine walk-throughs catch missing guards, faulty brakes, worn parts—before OSHA fines you or worse, before downtime eats your margins. Prevention isn’t luck. It’s method.